There are several performance specifications that are commonly used to describe the capabilities of hydraulic valves.
Here are some examples:
Flow rate: The flow rate is the amount of fluid that can pass through the valve per unit of time and is typically measured in gallons per minute (GPM) or liters per minute (LPM). The flow rate is determined by the valve size, the pressure drop across the valve, and the fluid viscosity.
Pressure rating: The pressure rating is the maximum pressure that the valve can handle, typically measured in pounds per square inch (PSI) or bar. The pressure rating is determined by the valve design, materials, and manufacturing process.
Leakage rate: The leakage rate is the amount of fluid that can pass through the valve when it is closed. A low leakage rate is important for applications where precise control of fluid flow is required.
Response time: The response time is the time it takes for the valve to open or close in response to a change in the control signal. A fast response time is important for applications where rapid changes in fluid flow are required.
Temperature range: The temperature range is the range of temperatures over which the valve can operate effectively and reliably. This is important for applications where the fluid or environment temperature may vary widely.
Duty cycle: The duty cycle is the percentage of time that the valve is open or closed over a given period of time. This is important for applications where the valve is required to operate continuously or for extended periods of time.
Overall, the performance specifications of a hydraulic valve will depend on the specific application and the requirements of the system. It’s important to carefully consider these specifications when selecting a valve to ensure that it will meet the performance requirements of the application.
How do I determine the appropriate valve size for my application?
Selecting the appropriate valve size for your application is important to ensure that the valve can handle the required flow rate and pressure drop.
Here are some steps to help you determine the appropriate valve size for your application:
Determine the required flow rate: The first step is to determine the required flow rate for your application. This can be calculated based on the amount of fluid that needs to be transported or the amount of work that the hydraulic system needs to perform. hydraulic valve manufacturers The flow rate is typically measured in gallons per minute (GPM) or liters per minute (LPM).
Calculate the pressure drop: The pressure drop is the difference in pressure between the inlet and outlet of the valve. This is determined by the flow rate and the resistance of the system components, such as pipes, hoses, and fittings. The pressure drop is typically measured in pounds per square inch (PSI) or bar.
Determine the valve coefficient: The valve coefficient, also known as the Cv value, is a measure of the flow rate through the valve at a given pressure drop. The Cv value is typically provided by the valve manufacturer and is based on the valve size, shape, and design.
Select the valve size: Once you have determined the required flow rate, pressure drop, and valve coefficient, you can select the appropriate valve size. This is typically done by consulting the manufacturer’s valve sizing charts, which provide the Cv values for different valve sizes and pressure drops. You should select a valve size that can handle the required flow rate and pressure drop while providing a Cv value that is close to the calculated value.
It’s important to note that selecting the appropriate valve size is not always straightforward and may require some experimentation or consultation with a hydraulic system expert. Additionally, there may be other factors to consider, such as the valve material, operating temperature, and environmental conditions.
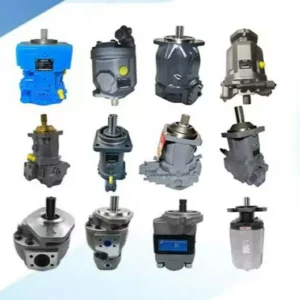