Cost Savings: One of the main reasons why some parents choose a baby diaper machine is to save money. With a baby diaper machine, parents can produce their own diapers at home, reducing the cost of constantly purchasing disposable diapers.
Environmental Benefits: Another reason why some parents choose a baby diaper machine is to reduce their environmental impact. By producing their own cloth diapers at home, parents can reduce the amount of waste generated by disposable diapers.
Customization: Baby diaper machines allow parents to customize the size, shape, and material of the diapers they produce. This can be particularly beneficial for babies with sensitive skin or unique physical needs.
Convenience: Finally, some parents choose a baby diaper machine for the convenience it provides. With a baby diaper machine, parents can produce diapers at home, eliminating the need to constantly purchase and dispose of disposable diapers. This can be especially beneficial for parents who live in areas where disposable diapers are not readily available or affordable.
However, it is important to note that using a baby diaper machine requires time and effort for cleaning, maintenance and production. Additionally, baby diaper machine cloth diapers produced from a baby diaper machine may not be as absorbent as disposable diapers, and may require more frequent changing. Parents should weigh the benefits and drawbacks of using a baby diaper machine before deciding whether it is the best option for their family.
How can I ensure that the cloth diapers produced by the machine are absorbent?
To ensure that the cloth diapers produced by your baby diaper machine are absorbent, there are several things you can do:
Choose the right fabric: The fabric you use for your cloth diapers can have a big impact on their absorbency. Look for fabrics that are known for their absorbent qualities, such as cotton or bamboo.
Use enough layers: To increase absorbency, you may need to use more than one layer of fabric. Consider using a diaper design that allows you to add or remove layers as needed.
Pre-wash the fabric: Before using the fabric to make diapers, pre-wash it several times to remove any residual chemicals or substances that may affect absorbency.
Use the right detergent: When washing cloth diapers, use a detergent that is free of additives and fragrances, as these can reduce absorbency.
Avoid fabric softeners: Fabric softeners can coat the fabric fibers, making them less absorbent. Avoid using fabric softeners when washing your cloth diapers.
Check for leaks: If you find that your cloth diapers are not absorbing as much as you would like, check for leaks or gaps in the diaper design. A well-fitting diaper will be more effective at absorbing moisture.
By following these tips, you can ensure that the cloth diapers produced by your baby diaper machine are absorbent and effective at keeping your baby dry. However, it may take some trial and error to find the right combination of fabric and design that works best for your baby’s needs.
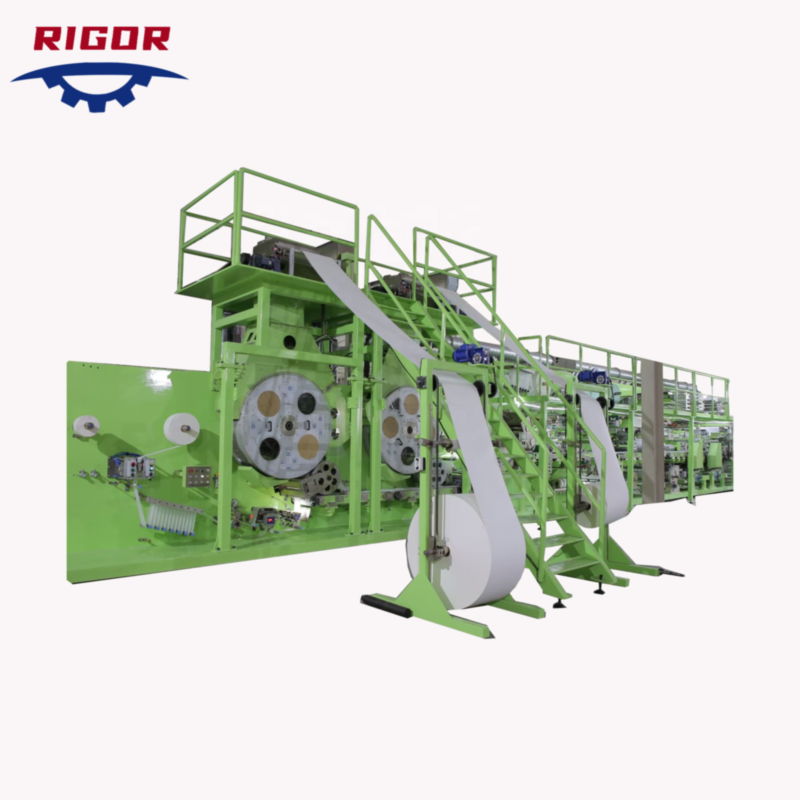